Construction Techniques
Prefabricated construction techniques encompass various approaches to assembling building components, each offering unique advantages and considerations. Understanding these techniques is essential for stakeholders involved in construction projects to select the most suitable approach based on project requirements, budget constraints, and scheduling considerations. Here are two primary construction techniques commonly used in prefabricated construction
On-site vs. Off-site Assembly
On-site Assembly
In on-site assembly, construction activities primarily take place at the project site, where building components are assembled and installed directly in their final location. While some prefabricated elements, such as precast concrete panels or structural steel beams, may be manufactured off-site and transported to the construction site, the majority of construction work occurs on-site. On-site assembly offers advantages such as greater flexibility in accommodating site-specific conditions and design modifications, as well as reduced transportation costs for large or heavy components. However, on-site assembly may result in longer construction timelines, increased labor costs, and potential disruptions due to weather conditions or site constraints.
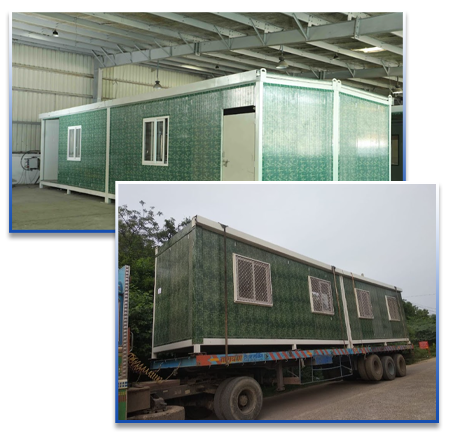
Off-site Assembly
In off-site assembly, building components are manufactured in a controlled factory environment away from the construction site and then transported to the site for assembly. Off-site assembly encompasses various prefabrication methods, including modular construction and panelized construction. Off-site assembly offers several advantages, including faster construction timelines, improved quality control, and reduced on-site disruption. By manufacturing building components off-site, construction activities can be completed concurrently with on-site site preparation, resulting in shorter overall project durations. Off-site assembly also minimizes weather-related delays and reduces labor costs associated with on-site construction. However, off-site assembly may require careful coordination for transportation and logistics, as well as additional planning for crane access and site access.
Integration with Traditional Construction Methods
Prefabricated construction techniques can be seamlessly integrated with traditional construction methods to create hybrid construction approaches that leverage the benefits of both approaches. For example, prefabricated building components such as wall panels or floor systems can be combined with traditional site-built elements to achieve a customized solution that meets project requirements. Hybrid construction approaches offer flexibility in design and construction, allowing for greater customization and adaptation to site-specific conditions. By integrating prefabricated components with traditional construction methods, stakeholders can optimize project efficiency, reduce construction timelines, and enhance overall project outcomes.
High-Quality Construction Outcomes.
Understanding the differences between on-site and off-site assembly techniques, as well as the integration possibilities with traditional construction methods, allows stakeholders to select the most appropriate approach for their construction projects. By leveraging the benefits of prefabricated construction techniques and integrating them effectively with traditional methods, stakeholders can achieve efficient, cost-effective, and high-quality construction outcomes.